The imagination of flying like a bird came to life on December 17, 1903. The Wright Brothers, Orville and Wilbur Wright, achieved the first powered flight in North Carolina with their aircraft, the Wright Flyer. The flight covered a distance of 120 feet and lasted for 12 seconds.
From here, there were a number of inventions in the field of aerospace. One of the most revolutionary inventions was the jet engine, also called the gas turbine engine. In this blog, we are going to learn about the science and engineering of the jet engine.
HISTORY OF JET ENGINE
- 120–150 BC : The idea of jet reaction was first demonstrated by Hero
- 1930: Sir Frank Whittle of England patents his design for a gas turbine for jet propulsion.
- 1939: In August, the company Ernst Heinkel Aircraft flies the first gas turbine jet plane.
- 1941: Sir Frank Whittle designs the first successful turbojet, the Gloster Meteor.
- 1942: Jumo 004, used in the Messerschmitt Me 262, the world’s first operational jet flight.
- 1948: The first turbojet breaks the sound barrier.
- 1949 : First use of turbojets for commercial service
- 1955 : First use of reheat to increase thrust of turbojet
WORKING PRINCIPLES OF JET ENGINE
Before we go into the workings of the jet engine, we first understand the principle of flight, or, as we can say, the primary forces behind a flight.
PRIMARY FORCES
- LIFT The force opposing gravity keeps the aircraft floating. This force is due to the aerofoil shape of aircraft. Aerofoil shapes create low air pressure above and high pressure below, which generates an upload force.
- WEIGHT is the gravitational force pulling an aircraft downward. To counter the weight, lift should be equal to or greater than the gravitational force.
- DRAG is the opposing force faced during the forward motion of the aircraft.
- TRUST It is the forward force required to propel the aircraft and counter the drag. The role of the jet engine is to provide trust, which in turn provides forward motion and lift.
KEY PRINCIPLES
Let us look at some key principles of science behind the operation of jet engines.
- Newton’s Third Law of Motion: The law states that “every action has an equal and opposite reaction”. In the context of jet engine, when high-speed gases are expelled from the rear of the engine, they provide equal force in the opposite direction, called thrust.
- Compressibility of Gases: The jet engine relies on the principle of fluid dynamics and the behavior of gases. The air is drawn in and compressed, which makes it denser. On expelling this compressed air, it can release a significant amount of energy.
- Bernoulli’s Principle: This principle states that as the speed of air (or fluid) increases, its pressure decreases. In a jet engine, the shape of the aerofoil blades in the compressor and turbine is designed to take advantage of this principle. The air is accelerated as it passes over the curved blades, causing a decrease in pressure, which helps to compress the incoming air and generate thrust
- Conservation of Momentum: The conservation of momentum is another critical principle. As air is drawn into the engine and accelerated by the compressor, its momentum is increased. When the air is expelled at high speed from rear, it carries away a significant amount of momentum, creating thrust and propelling the aircraft forward
- Combustion: fuel is mixed with compressed air and ignited in the combustion chamber. The combustion of a mixture of fuel and air is a chemical reaction that releases a large amount of heat energy, which in turn increases the temperature and pressure of the exhaust gases. This process is essential for generating the high-speed exhaust required for thrust
- Thermodynamics: also follow the principle of thermodynamics, specifically the Brayton cycle. In this cycle, air is compressed, heated, expanded, and then exhausted. The compression and heating stages increase the energy, while the expansion and exhaust stages convert this energy into useful thrust.
STAGES OF JET ENGINE
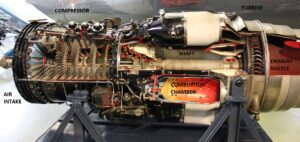
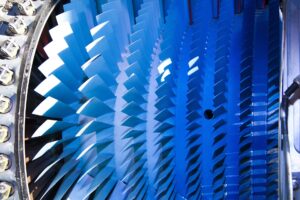
Here is a brief overview of how jet engines operate:
- Air intake: it is the front of a jet engine, from which a large amount of air is drawn inside the engine.
- compression: Once air enters the engine, it is compressed by the compressor. The compressor may be axial or centrifugal. The work of the compressor is to reduce the volume of air and increase the pressure.
- combustion: in combustion, highly compressed air is mixed with fuel (jet fuel) and ignited. Due to the combustion of gases, heat is produced, and the expansion of gases takes place. Temperatures may rise to up to 1700 degrees Celsius inside the combustion chamber of a commercial jet engine.
- Turbine: The high-speed exhaust gases flow over a series of turbine blades at the rear of the engine. These blades are connected to the same shaft as the compressors at the front of the engine. As the exhaust gases pass over the turbine blades, they cause the turbine to spin, which in turn spins the compressor blades.
- Exhaust nozzle: exhaust gases with high temperatures and pressure exit the engine from the exhaust nozzle. This nozzle plays an important role in providing the required thrust, it is specially shaped as per the thrust requirement.
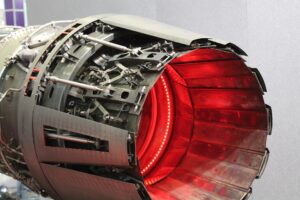
WORKING OF TURBINE JET ENGINE
The workings of a jet engine can be described in four stages: suck, squeeze, bang and blow.
- The engine sucks a large amount of air at a very high rate, which varies from engine to engine. This air is used in two ways: one to produce thrust and another to cool down the engine by flying over the surface.
- The second stage is squeezing. Sucked air is then compressed by a compressor, which compresses the air and reduces the volume, hence increasing the pressure. As we earlier discussed, the to types of compressors are centrifugal and axial. Centrifugal compressors can increase the total pressure of the air by a factor of 4, and axial compressors can only increase the pressure by a factor of 1.2. The axial compressor consists of rows of stators (they do not rotate) and rotors (they connect with the shaft and rotate at high speed). While centrifugal compressors have specially designed blades, they also have important viscous and compressibility effects.
- The third stage, called bang, after the compressor, compressed air is passed to the combustion chamber. Here, compressed air is mixed with jet fuel (supplied with a spray nozzle) and makes a highly combustable mixture. The chamber is made up of material that can stand high temperatures.
- The last stage, called blow, occurs when air exits the combustion chamber. It has a high temperature and pressure before leaving the engine. This high-velocity air strikes the specially designed blades of the turbine. Turbine blades and compressors are placed on the same shaft. Some energy of exhaust gases is used to rotate turbines, which in turn rotate compressor blades and intake fans.